
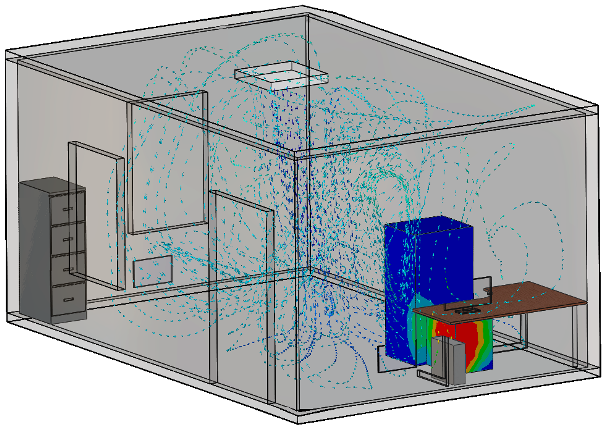
#Solidworks flow simulation system requirements full
With the multiphysics simulation software SimulationX, you are in full control of a vehicle’s electronics and mechatronics interactions. Integrate with requirements management and system architecture to create a traceable model-based systems engineering (MBSE) framework that fulfills strong certification requirements for safety and reliability supported by virtual testingīenefits of SimulationX for Vehicle Development.Assess safety and reliability with fault tree analyses (FTA) and failure mode and effect analyses (FMEA) based on system models.Develop reliable drive and altitude control systems of satellites and spacecraft to ensure design and operation for extreme conditions.Model and simulate complex systems towards hydrogen-based aviation.Equip your training simulators with realistic and physically correct behavior.Develop, optimize, and control test benches for components and systems for aircraft and spacecraft.Design energy efficient environmental control systems.Create next-generation aircraft actuation systems with small, lightweight, powerful batteries, electric motors and generators.©2018 - 2021 BestMoldComponents.Benefits of SimulationX for Aerospace Applications
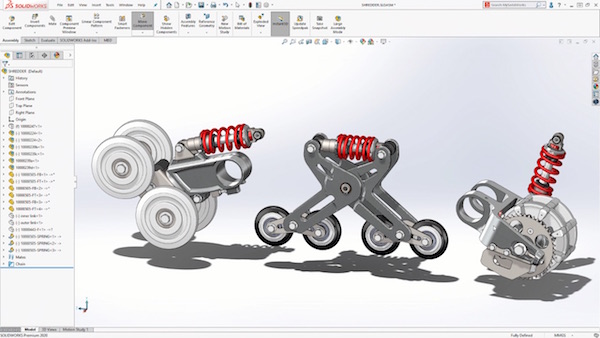
The time taken for the moldflow simulation can decrease by up to 40%. For Autodesk Moldflow Insight, it is mhb3d.exe. Only the process of moldflow simulation should be excluded. Of course, the antivirus software should not be completely disabled. Do you know the absolute cheapest way to increase the performance of your workstation? Disable virus scanning can make a big difference. It is a few years since we tried it last but our experience is positive and it worked very well. If you want an even faster simulation a solution can be dual processors. The analysis of 13.5 million tetras gave a 25 GB file size. Mold flow simulation with 13.5 million tetras took 40 hours and used up to 31 GB of RAM. Mold flow simulation with 3 million tetras took almost 13 hours and used up to 11 GB of RAM.ģD meshing with 13.5 million tetras took 42 minutes and used 11 GB of RAM. The above Dell workstation and Autodesk Moldflow Insight 2018 R2 have been used.ģD meshing with 3 million tetras takes just over 8 minutes and used 5 GB of RAM. Some guideline values based on recent simulations will be shown below. Estimating the time required to prepare your 3D model with a 3D mesh and simulation is not easy. You do not know in advance how long it will take.ĭoes your workstation have too little RAM to cope with the simulation you are planning to perform? It is very ineffective having to interrupt after 15-20 hours of simulation due to such a thing. For the actual mold flow simulation the same applies. You cannot know in advance how many tetras you will get before you mesh your 3D model. When it comes to mold flow simulation it is interesting to know how long some tasks might take. Hardware for mold flow simulation and mold flow analysis. To ensure you are always working with a SolidWorks supported and optimized system, check out SolidWorks recommended hardware and recommended system requirements. It is a set of tests that compares your system against others. Here you will find information about doing a SolidWorks performance test. Avoid dual processors because they simply do not work well with SolidWorks. Our experience is that SolidWorks works best with a single processor and high clock frequency. The recording has been made with the resolution 1920x1200 30 fps and there have been no problems. During the recording SolidWorks mold assembly has been fully resolved with more than 10,000 configurations in the associated parts. It is equipped with an Intel (R) Xeon (R) E5-1650 v3 3.5GHz CPU, a Nvidia Quadro K4200 graphics card and 32GB RAM. In the video tutorial a Dell Precision Tower 5810 Workstation has been used. Autodesk moldflow insight from Autodesk and SolidWorks from Dassault Systemes are examples of this. This means it has been tested with specific software to run optimally. Your workstation should have an ISV (Independent Software Vendor) certification. To handle the most demanding tasks for injection molding mold design and mold flow simulation software it is important that your hardware has the best optimal performance possible as you should be able to rely on it when you really need it. Best Mold Components Component Creator Injection molding software
